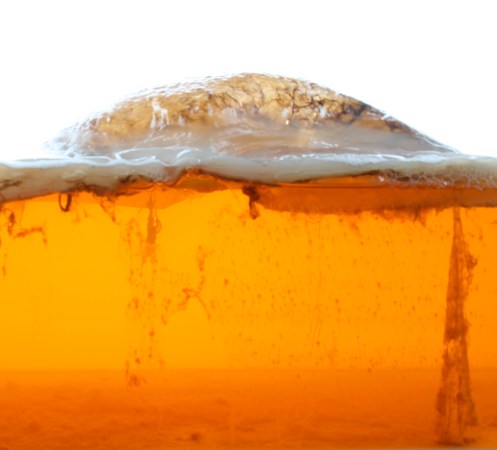
What might our clothes look like in 50 years? When textile designer Suzanne Lee was researching her book, Fashioning the Future, she found the most interesting answers to that question when she looked beyond the traditional borders of fashion design. Beyond cut, color and cloth, our style in 50 years will be driven by new materials from the corners of science. With biologists, engineers and materials scientists, she realized, she could create an entirely new strain of fashion.
In 2003, Lee met materials scientist David Hepworth, founder of the Scotland-based firm Cellucomp, which develops materials made from non-hydrocarbon-based feedstock. His advice: “Instead of thinking about fiber production from a source like cotton in a field — an agricultural approach — we could look to living organisms like bacteria to produce fibers for us.”
So that’s what they have done. Hepworth and Lee started growing materials, at first in Hepworth’s garage and Lee’s bathroom. Ten years later, Biocouture was born. Based in London, the company works with scientists to bring living, bio-based materials to fashion.
I caught up with Lee, who is a TED Fellow, over the phone to talk to her about her clothes and collaborations. Below is an edited transcript of our conversation.

What’s wrong with the materials traditionally used in fashion?
It’s actually not so much the materials; it’s the whole approach to manufacturing. An incredibly long and complex supply chain is involved in producing a piece of clothing. So there’s the huge toxicity and environmental impact of the production of clothing, and there’s also a massive social one.
As the Biocouture project developed, what became really interesting to me was how to address the pressing environmental issues around garment and fiber production, to think about more efficient ways to manufacture a garment. This wasn’t initially about trying to bring specific extra functionality to fashion, it was trying to re-think a system, and imagine if there was a more efficient and sustainable way.
Is your fashion more efficient than other clothing?
That’s an incredibly complex answer. Yes, it is, but it’s so beyond anything that currently exists that it becomes very challenging. The garments we create are made using fermentation. I’m essentially proposing moving to a model that’s closer to brewing or the food industry than to a textile factory.
That’s a massive conceptual and industrial shift, and there are many challenges associated with that. Things like the cost of the feedstock that you’ll feed your biological organisms to make these materials for you. That gets into a question of geography and where feedstock is abundant.

So … you’re feeding your clothing? What does that even mean?
Yep! Right now you can take an organism — I would use a bacteria — to produce a cellulose fiber. If we actually design the organism itself, we have full, final control over how that fiber is formed and its functionality. Right now we’re thinking about how you might combine something like a yeast cell not only to produce fiber but also to make the fiber hydrophobic.
In my process, the thing that feeds the bacteria is sugar. And sugar comes in lots of forms, but in certain parts of the world there are agricultural waste streams that are sugar-abundant, and they’re much cheaper. So we’re thinking about how we can bring the cost down so we’re not using food-grade sugar. How can we identify a nutrient source from the waste of another industry?

It seems like companies that can produce clothing from sketch to rack in a matter of days would surely have an advantage over this complex process. How can you compete with them — and their incredibly thin margins?
So-called “fast fashion” has got cheaper and cheaper, and people have got used to paying less and less, so the actual value of a garment today is far less than it was ten and 20 years ago. And, of course, the value of the material that goes into that product is incredibly low, so you’re competing with oil-based fibers like polyester, which are super cheap. It becomes very difficult to be economically competitive. The savings in terms of water and environmental impact are mind-blowing, but the underlying issue of how to deliver something that will compete with incredibly cheap synthetics is difficult to answer.
So this isn’t necessarily something that will make it to the mass market in the near future?
No. Biocouture, for me, was the beginning of a journey. The work that I started [with Hepworth] began a wider conversation around how we might harness living organisms to make materials for us. Since then I have been approached by scientists working on materials using different types of organisms. I was initially using yeast and bacteria, but then I became aware of people using mammalian cells, fungi and so on.
I’m really excited to be thinking about not just one material, but this new landscape of living materials. And about what that means for design, for manufacturing, for us all in terms of products. Some really interesting new possibilities could emerge when we start to see a convergence of material with things like well-being or functionality.
For example, in synthetic biology, you can produce anti-malarials that could be used in pharmaceuticals. But could we get bacteria to spin us a thread that also has anti-malarial properties? We can start to build layers of functionality into these materials.
So this is about much more than fashion.
We don’t need fashion. Fashion is not essential to our survival, right? There are things within the fashion-textile arena that we might hope could be produced in a more efficient or environmentally friendly way. But we can think more broadly about how we can design a better world. There are really exciting applications for these kinds of materials. For instance, how can we think about using living materials to create more sustainable architecture or the interior of a car?
How do you find people to collaborate with and borrow from? How do you persuade researchers they should help?
There’s an economic imperative for scientists and academics to find nearer-to-market applications for a lot of their work. Here in the UK, there’s been increasing pressure for people to explain the value of their scientific research to the general public. I find, increasingly, that those people are incredibly welcoming to designers who have been thinking about different aspects of science and how these might be applied.

“Questions Worth Asking” is a TED editorial series; this week we asked the question, “Can I borrow that?” to dig into themes of cross-disciplinary innovation and idea-sharing. See also Seth Godin’s op ed, “Why I want you to steal my ideas,” and a story about SkyBox Imaging, a company using unexpected technology to build a new type of satellite.